Various industrial processes, particularly the systems that require frequent access to pressure vessels and pipelines find the Quick opening closures (QOCs) an essential component. These closures are designed to enable fast, safe, and efficient opening and closing of vessels. The presence of these closures can help in significantly reducing downtime during maintenance, inspection, or cleaning.
Pressure vessel quick opening closures are widely used in industries such as oil and gas, chemical processing, and water treatment, where operational efficiency is the most critical. With diverse quick opening closure types available in the market, including threaded, clamp-ring, and yoke designs, industries can choose solutions tailored to specific applications and pressure ratings. Quick opening closure manufacturers such as Sungov Engineering, focus on delivering high-performance closures that ensure safety, reliability, and compliance with industry standards, making QOCs a vital part of modern industrial operations.
What are the Common Causes of Wear and Tear of the QOC
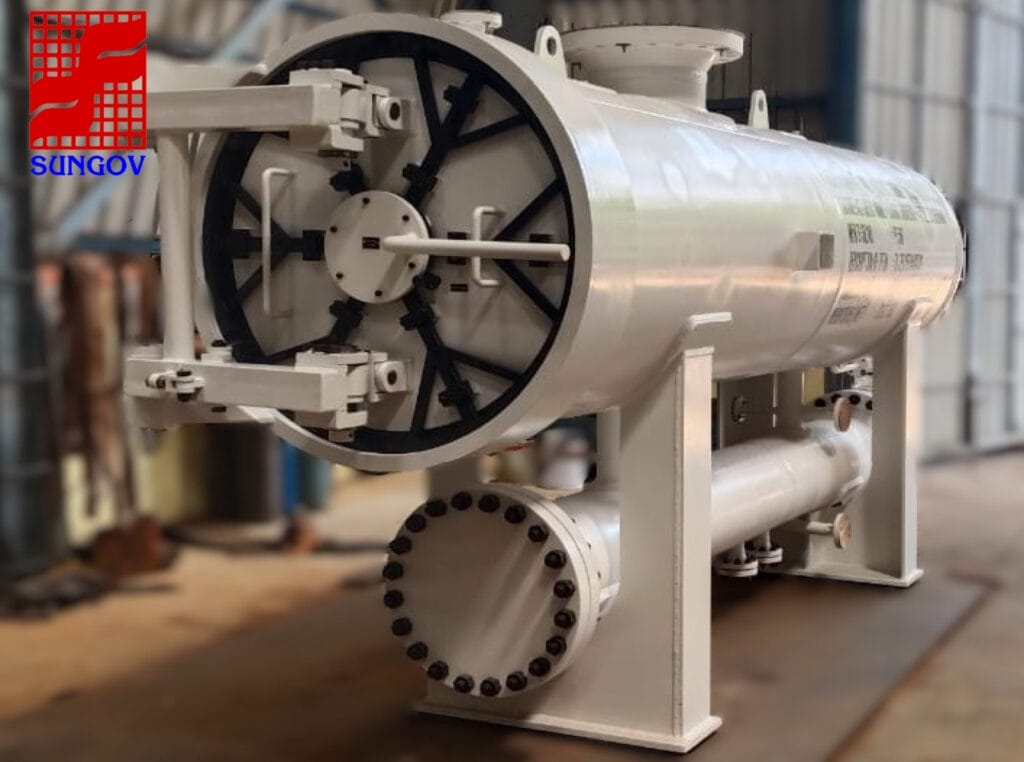
Quick opening closures (QOCs) play a critical role in facilitating efficient access to pressure vessels and pipelines, but they are not immune to wear and tear over time. One of the primary causes is frequent usage, particularly in applications that involve high-pressure environments, such as those using pressure vessel quick opening closures. The repeated opening and closing cycles can stress components such as seals, gaskets, and locking mechanisms, leading to degradation. Environmental factors that include exposure to corrosive chemicals, moisture, or extreme temperatures, can also exacerbate this wear, especially if the closure is not made from corrosion-resistant materials.
Another significant contributor to the wear is improper installation or misalignment of the QOC, as it can cause uneven force distribution across the closure. This leads to mechanical strain and eventual failure. When you choose a mismatched quick opening closure type you can impact their longevity; for example, some designs may be more prone to wear in certain applications if not properly matched to operational requirements.
Sungov Engineering always emphasizes the importance of routine maintenance, such as inspecting seals, lubricating moving parts, and ensuring proper alignment, to minimize these issues.
Ignoring these preventive measures can result in diminished performance, safety risks, and costly downtime. This only highlights the need for high-quality closures that are tailored to specific industrial needs.
What are Some Routine Inspection Guidelines for Quick Opening Closure (QOC)
We have listed some routine inspection guidelines that must be followed:
- Examine the closure for visible signs of wear, cracks, corrosion, or misalignment. This can be done by visible observation
- Inspect seals and gaskets for cracks, brittleness, or wear
- Look for signs of rust or chemical corrosion on the surface and internal components. You may need to pay special attention to areas that are exposed to moisture or harsh chemicals
- Ensure the closure is properly aligned with the pressure vessel or pipeline opening
- Inspect bolts, hinges, and other fasteners for wear or loosening. You may even want to tighten or replace as necessary to ensure proper function
- Check for adequate lubrication of moving parts, such as hinges and locking mechanisms. It is always recommended to apply manufacturer-recommended lubricants to prevent friction and wear
- Verify that the closure maintains its pressure rating and structural integrity during operation
- Test safety locks, vent systems, and other protective features to ensure functionality
- Clean the closure to remove debris, dirt, or chemical residues
- Keep detailed records of inspections, noting any issues, repairs, or replacements made.
What are some of the Operational Best Practices for Quick Opening Closures (QOC)
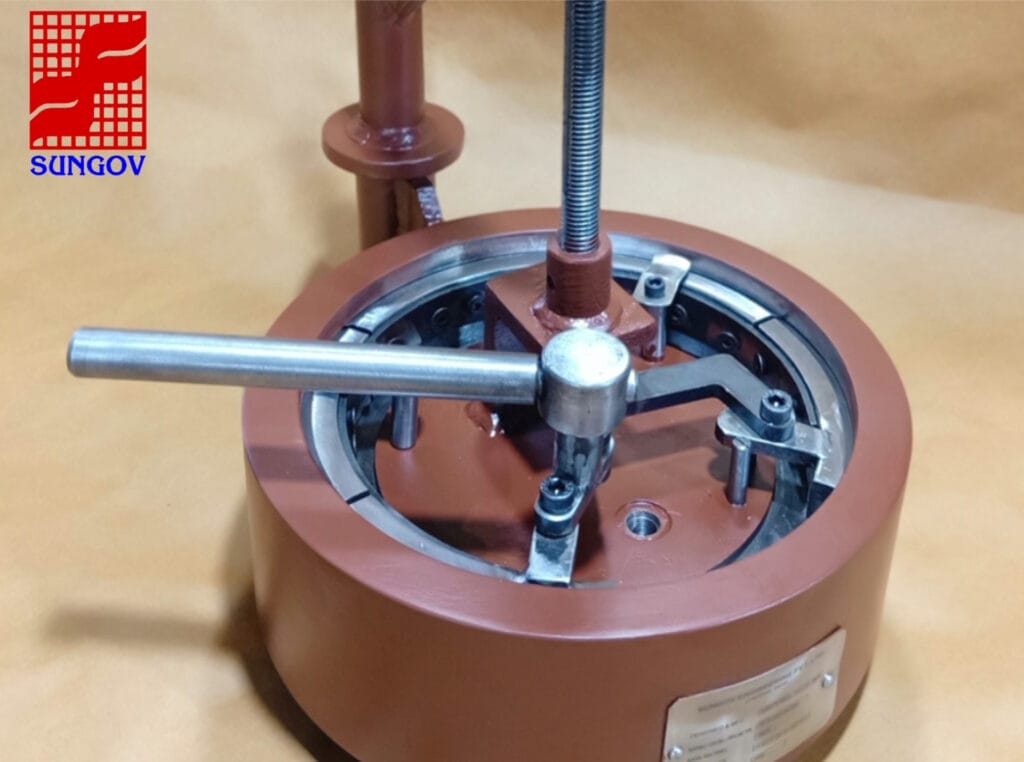
Implementing operational best practices is key to ensuring the safety, efficiency, and longevity of quick opening closures (QOCs). These closures are critical in industries requiring frequent access to pressure vessels or pipelines, and proper handling is essential to prevent wear, damage, or safety risks. It is always best to follow the manufacturer’s guidelines for operating the closure, as different quick opening closure types may have specific requirements.
Ensure that the pressure inside the vessel is fully relieved before attempting to open the QOC to avoid hazardous situations. Operators should be trained in proper opening and closing techniques, including avoiding excessive force, which can damage components such as seals, gaskets, or locking mechanisms. Regularly check the alignment of the closure to the vessel opening, as misalignment can cause uneven stress and compromise the closure’s performance.
During operation, maintain a clean working environment to prevent debris or contaminants from interfering with the closure’s functionality. It is always best to use appropriate tools and avoid unauthorized modifications to the closure or its components. When you adhere to these best practices, coupled with routine maintenance, you can ensure the reliable performance of QOCs and reduce the risk of operational downtime or costly repairs.
Choosing the Right Spare Parts for Quick Opening Closures (QOC)
Selecting the correct spare parts is critical to maintaining the performance and safety of quick opening closures (QOCs). When there is a use of incompatible or substandard parts, the integrity of the closure is compromised, leading to operational inefficiencies or safety hazards. As a first step in choosing the right spare parts it is vital to consult the original equipment manufacturer (OEM) or the quick opening closure manufacturers. OEM parts are specifically designed to meet the specifications of the closure and ensure compatibility with its quick opening closure types.
Focus on high-wear components such as seals, gaskets, locking mechanisms, and hinges, as these are often subject to frequent replacement due to regular use. You can ensure that replacement parts are made from materials that can withstand the operational environment, including exposure to high pressure, extreme temperatures, or corrosive substances. For example, spare parts for a pressure vessel quick opening closure must be capable of maintaining a secure seal under significant stress.
Maintaining an inventory of critical spare parts reduces downtime by allowing for immediate replacement when needed. Additionally, always verify the part numbers, dimensions, and materials to avoid mismatches that could compromise the closure’s functionality. By investing in high-quality, manufacturer-approved spare parts, you can extend the lifespan of your QOC and ensure reliable operation over the long term.