The Evolution of QOC Technology in High-Pressure Environments
The way industries manage access to pressure vessels in high-pressure environments has changed drastically, thanks to the development of Quick Opening Closure (QOC) technology. What initially was a time-consuming and labor-intensive process, opening and closing vessel closures are now faster, safer, and more reliable because of quick-opening closure designs. Modern QOC systems now feature advanced safety interlocks, robust sealing mechanisms, and user-friendly interfaces, drastically reducing downtime and enhancing workplace safety.
Over time, various quick-opening closure types have emerged, such as clamp-style, bayonet, and hinged door closures. Each of these closures can be tailored to specific industrial applications. These innovations not only improve efficiency, but they also ensure compliance with stringent safety standards in industries like oil & gas, chemical processing, and filtration systems.
Key Challenges in High-Pressure System Access and Maintenance
In high-pressure systems, there is a unique set of challenges with regard to maintenance and access, especially when safety, speed, and efficiency are involved. With traditional closures, there is always a need for extensive downtime and specialized tools. In addition to this, traditional methods are labor-intensive procedures that increase operational costs and safety risks. This is where modern quick-opening closure (QOC) technology gains popularity.
However, even with advancements in quick-opening closure design, challenges such as ensuring leak-proof sealing, maintaining structural integrity under extreme pressure, and preventing accidental openings persist. Selecting the right quick-opening closure type for a specific application—whether it’s a clamp, bayonet, or swing-bolt design—is critical to overcoming these issues. To add to this, maintaining these closures in harsh environments requires durable materials and precise engineering to ensure long-term performance and compliance with industry safety standards.
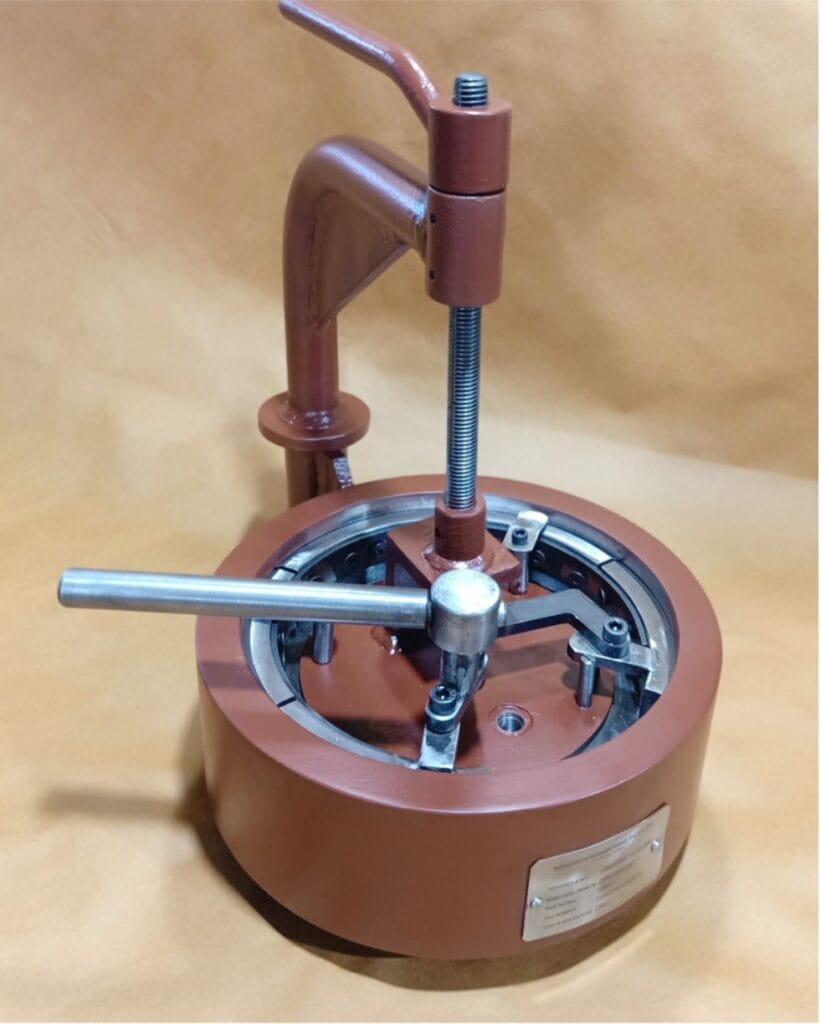
Innovations Driving the Next Generation of QOC Designs
As industrial operations grow more demanding, innovation in quick opening closure (QOC) technology is rapidly advancing to meet the needs of high-pressure environments. As we move on to the next generation of quick-opening closure designs, we can see the focus shift that is clearly on enhancing both safety and operational efficiency, particularly for applications that involve pressure vessels. To improve the durability and, as a consequence, to reduce maintenance, newer materials, such as corrosion-resistant alloys and advanced composites, are adopted. There are advancements in design, such as automated locking systems, integrated pressure release mechanisms, and ergonomic handling. These are all adapted to streamline operation while minimizing human error.
These advancements are also making it easier to customize quick-opening closure types for specific industry requirements, whether it’s a hinged door for ease of access or a clamp-style closure for space-constrained systems. We are also noticing digital technologies being integrated with mechanical components, smart QOCs equipped with sensors, and IoT connectivity. These are setting new benchmarks for safety, performance, and real-time monitoring in high-pressure systems.
Material Advancements for Greater Durability and Performance
As the Quick Opening Closures have evolved over time, the selection of materials has emerged as an important factor in both durability and performance. QOC designs lately are leveraging advanced materials such as duplex stainless steels, Inconel, and corrosion-resistant alloys. These help in withstanding extreme pressures, temperatures, and aggressive chemical environments typically found in pressure vessel applications. With these materials, there are not only chances of extended service life of the closures but also a reduction in maintenance frequency and improvement in safety margins.
In addition to this, innovation in surface treatments and coatings adds another layer of protection, especially for closures used in offshore and highly corrosive settings. With the increasing need for customized quick-opening closure types, material versatility has become essential, allowing engineers to tailor each closure to specific industrial requirements without compromising on strength or safety.
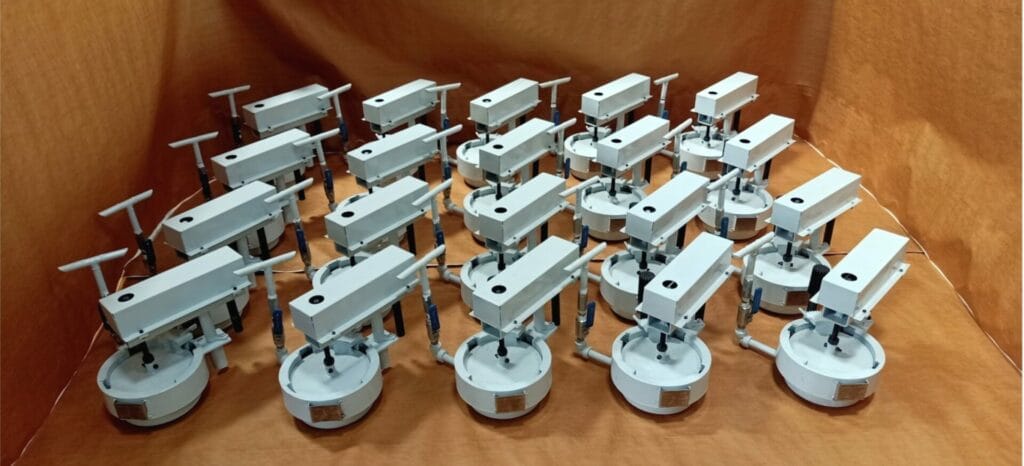
Conclusion:
As industries evolve toward more efficient, reliable, and safer operations, quick opening closures (QOCs) are set to play a pivotal role in shaping the future of oil and gas, filtration, and energy sectors. With increasing emphasis on minimizing downtime, enhancing safety, and optimizing maintenance procedures, the demand for innovative quick-opening closure designs is expected to rise significantly.
Whether it’s for natural gas filtration, chemical processing, or power generation, the availability of diverse quick-opening closure types, engineered with advanced materials and smart technologies, ensures that each system operates at peak performance. As industries continue to pursue efficiency and sustainability, QOCs will remain a critical component in meeting tomorrow’s operational and regulatory challenges.
The location of installation of these Quick Open Closures (QOC) is in India and Kuwait.