Understanding Gas-Liquid Separation: An Overview
Imagine a natural gas processing plant that runs smoothly, delivering high-quality gas to its end users. What do you think is quietly working behind the scenes to ensure this kind of efficiency? If you didn’t already know it, it is a gas-liquid filter separator.
These essential systems are designed to remove liquids and fine particles from the natural gas stream and when doing so they protect the downstream equipment and maintain product quality. It is very important to have a well-sized natural gas filter separator—it must handle the gas flow rate, pressure, and composition to operate effectively. When the operators understand the fundamentals of gas-liquid separation, they can choose and size their filter separators wisely. Thereby ensuring reliability, efficiency, and compliance with industry standards. As this blog goes further you will learn more about the importance of coalescing filters in natural gas processing.
The Science Behind Coalescing Filters
Has it ever crossed your mind how a natural gas stream becomes clean enough to meet stringent industry standards? The answer lies in the science behind coalescing filters. This is a critical component of any gas-liquid filter separator. These filters operate by forcing tiny liquid droplets and particles in the gas stream to combine—or coalesce—into larger droplets that are then easier to remove. When this process is in place it ensures that your natural gas filter separator not only protects downstream equipment but also delivers clean, high-quality gas.
It is vital to choose the right coalescing filter and size it appropriately for your natural gas filter separator. When doing so, you must consider factors such as flow rate, gas composition, and pressure drop. That’s where companies like Sungov Engineering excel. Their advanced coalescing filters are specifically designed for precision performance, offering exceptional efficiency and durability. With Sungov’s expertise, you can confidently size your natural gas filter separator for maximum effectiveness. When you understand the science behind these filters, you’re one step closer to optimizing your gas-liquid separation process.
Key Components of a Coalescing Filter System
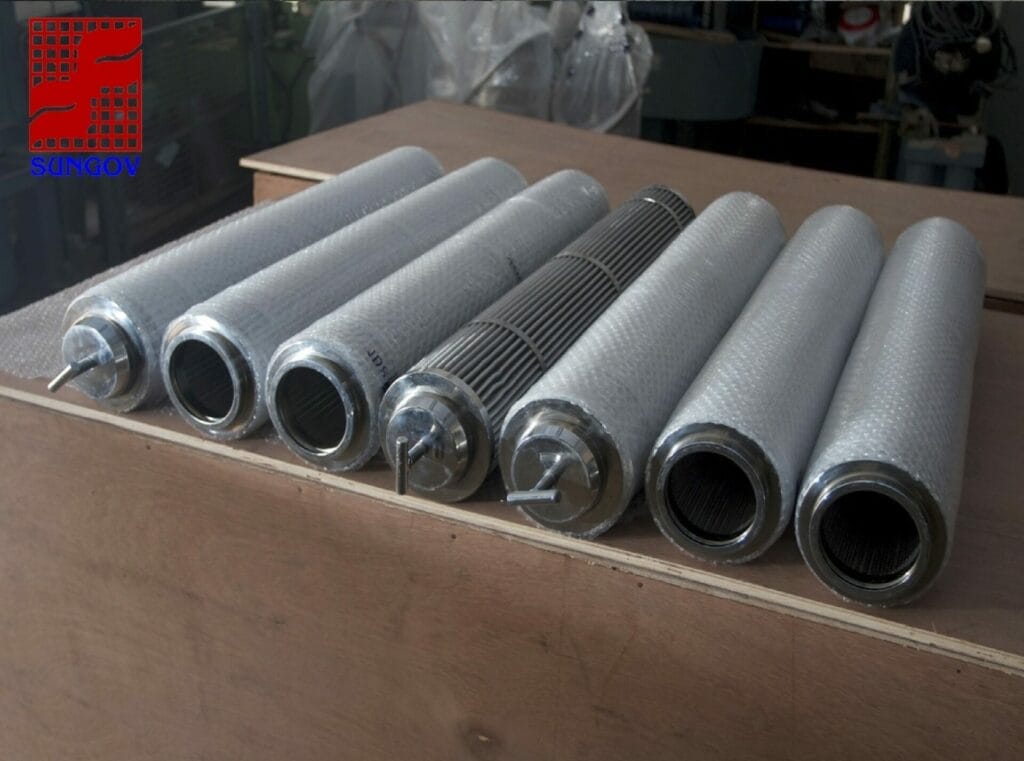
What is it that makes a coalescing filter system so effective in a gas-liquid filter separator? It’s all about the right components working together. At the heart of a natural gas filter separator lies the coalescing element. This is a specialized filter that is designed to capture and combine fine liquid droplets. With the help of layers, this element uses carefully engineered fibers to encourage small droplets to merge into larger ones that can be easily removed.
But it is not only the coalescing element that works alone. The system also includes a separator section, which removes the coalesced droplets from the gas stream. Other critical components of this system include the inlet and outlet diffusers, which manage gas flow to prevent turbulence, and the drainage mechanism that collects and disposes off separated liquids efficiently.
When you size your natural gas filter separator correctly it ensures that these components function harmoniously. As mentioned before, there are factors like gas flow rate, pressure, and contaminant load that must be given careful consideration during the design and selection process. A well-sized filter system not only guarantees optimal performance but also minimizes operational costs and extends the life of your equipment. Understanding these key components is the first step to mastering gas-liquid separation!
Applications of Coalescing Filters in Natural Gas Processing
Coalescing filters play a pivotal role in natural gas processing. They ensure that the gas meets quality and safety standards. These filters are a critical part of any gas-liquid filter separator and are used in applications ranging from removing liquid hydrocarbons and water vapor. Imagine a pipeline transporting natural gas—without a well-designed and properly sized natural gas filter separator, contaminants could damage equipment, reduce efficiency, and even compromise the gas quality delivered to end users. By integrating coalescing filters into processes such as gas dehydration, compression, and transmission, operators can protect downstream systems and ensure compliance with environmental regulations.
Common Challenges in Gas-Liquid Separation and How Coalescing Filters Address Them
Gas-liquid separation isn’t without its challenges. Operators often face issues like high liquid loads, fine aerosol mist, fluctuating gas flow rates, and the risk of contaminants bypassing the system. Without an effective solution, these problems can lead to equipment corrosion, reduced efficiency, and costly downtime. Enter the coalescing filter, a game-changer in any gas-liquid filter separator.
Coalescing filters excel at tackling these challenges. Their advanced design captures even the tiniest liquid droplets and particles. They then combine these droplets into larger ones that are easier to remove. This precision minimizes liquid carryover and ensures cleaner, drier gas for downstream applications. Proper natural gas filter separator sizing is crucial here—it ensures the system can handle varying flow rates and contaminant loads without compromising performance.
By incorporating well-designed coalescing filters, such as those found in a high-quality natural gas filter separator, operators can achieve consistent results even in demanding conditions. The right filter system transforms these challenges into opportunities for improved efficiency and reliability, keeping your natural gas processing on track.
How to Select the Right Coalescing Filter for Your Facility
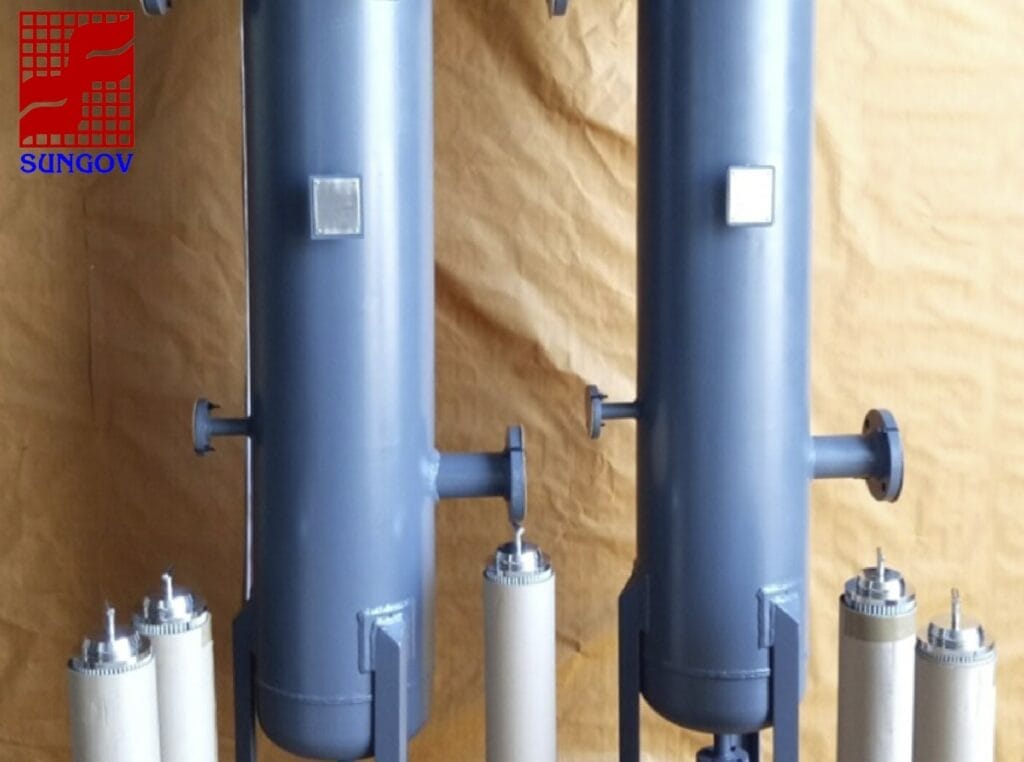
Choosing the perfect coalescing filter for your gas-liquid filter separator can feel overwhelming, but it’s a crucial step in optimizing your natural gas processing system.
The first step? Understand your specific needs. Are you dealing with liquid hydrocarbons, water vapor, or fine particulates? Identifying the contaminants in your gas stream is key to selecting a filter that’s up to the task.
Proper natural gas filter separator sizing comes next. Factors like gas flow rate, pressure, and contaminant load must be accurately assessed to avoid inefficiencies or costly overdesigns. An undersized system might struggle with performance, while an oversized one could lead to unnecessary expenses.
Here’s where Sungov Engineering can make all the difference. Renowned for their innovative gas-liquid filter separator solutions, Sungov Engineering offers high-performance coalescing filters designed to meet the unique demands of your facility. Our team ensures you choose the properly sized filter and help you achieve maximum efficiency and reliability.
Don’t leave your gas-liquid separation to chance—partner with experts like us to protect your equipment, enhance gas quality, and streamline operations. With the right guidance, finding the perfect coalescing filter is easier than you think!