Understanding Natural Gas Contaminants
For the sake of operational efficiency and longevity of equipment, it is vital to maintain purity when it comes to natural gas processing. Contaminants such as dust, rust, oil mist, and water can compromise system performance. This can lead to increased maintenance costs and potential equipment failures. This is where a natural gas filter cartridge plays a critical role in removing impurities before they cause damage. From stainless steel filter cartridges designed for high-pressure applications to liquid cartridge filters that effectively separate water and hydrocarbons, selecting the right filtration solution ensures optimal system performance. Understanding the types of contaminants present in natural gas is the first step in choosing the best filter cartridge for your industry.
Types of Natural Gas Filter Cartridges
It is very important to choose the right natural gas filter cartridge to ensure efficient filtration and maintain system reliability. There are various types of filter cartridges available in the market and each one of them is designed to remove specific contaminants such as particulates, liquids, and aerosols. We have listed below the main types of natural gas filter cartridges that are used in different industrial applications.
Particulate Filter Cartridges
- Designed to remove solid contaminants like dust, rust, and pipe scale
- Prevents clogging and erosion of downstream equipment
- Available in different micron ratings to capture fine particles
- Commonly made of materials like pleated synthetic fibers, cellulose, or stainless steel.
- Used to remove fine liquid droplets (aerosols) from natural gas
- Works by merging small liquid droplets into larger ones, which can then be drained away
- Highly effective in eliminating oil mist, water, and liquid hydrocarbons
- Typically made of borosilicate glass microfiber or synthetic media for high efficiency.
- Specifically designed to remove free liquids from the gas stream
- Prevents corrosion and damage to compressors, turbines, and other critical equipment
- Available in depth-type or pleated configurations, depending on application needs
- Made from materials such as polypropylene, fiberglass, or stainless steel.
Activated Carbon Filter Cartridges
- Used for the adsorption of oil vapors, odors, and dissolved contaminants in gas streams
- Ideal for applications requiring ultra-pure gas
- Typically made with a combination of carbon granules and support media
- Helps in removing trace hydrocarbons, sulfur compounds, and volatile organic compounds (VOCs).
Stainless Steel Filter Cartridges
- Designed for high-temperature and high-pressure applications
- Ideal for harsh environments with corrosive gases or extreme operating conditions
- Reusable and cleanable, offering a long service life
- Available in sintered, woven, or pleated stainless steel mesh configurations.
What are the Key Selection Criteria for Filter Cartridges
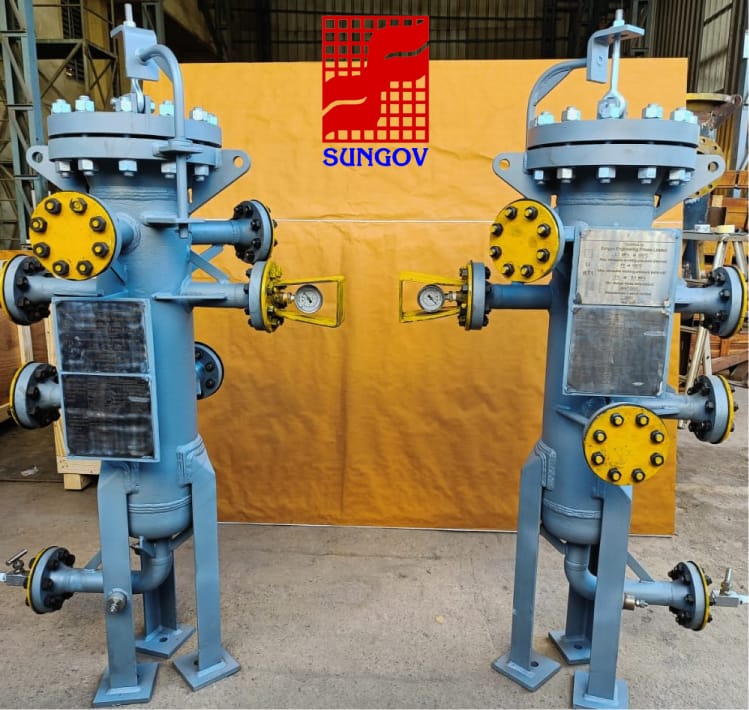
When selecting filter cartridges for applications such as natural gas filtration or liquid filtration, there are several key selection criteria that must be considered to ensure optimal performance and longevity. We have listed a few essential factors below:
Material Compatibility: It is very important to choose the right material for filter cartridge, such as stainless steel for high-temperature or corrosive environments. Stainless steel filter cartridges are robust and resistant to damage, making them ideal for demanding applications, including natural gas filtration.
Particle Size Removal: Different applications require different filtration ratings. When dealing with natural gas, it is very important to ensure that the filter cartridge can effectively remove particulates of specific sizes, preventing contamination and ensuring compliance with regulatory standards. For liquid cartridge filters, the pore size should align with the intended application to achieve the desired level of purity.
Flow Rate: Evaluate the required flow rate for the application. The selected filter cartridge must accommodate this flow rate without causing excessive pressure drop. A stainless-steel filter cartridge often has a higher flow capability compared to other materials.
Temperature and Pressure Ratings: High-performance filter cartridges should be rated for the intended temperature and pressure conditions. Filters used in natural gas applications need to withstand varying conditions without compromising the filter integrity.
Surface Area: A larger surface area on filter cartridges typically enhances filtration efficiency and reduces the frequency of replacement. This is especially important for liquid cartridge filters, where maintaining flow rates is critical.
Chemical Compatibility: The selected filter material must be compatible with the filtered fluids. For example, when using natural gas filter cartridges, ensure that they can handle the chemical composition of the gas without degrading.
Filter Lifespan: Consider the expected lifespan of the filter cartridges based on the application. Some filters may require more frequent changes due to higher contamination loads, while others can offer extended service life.
Regulatory Compliance: Ensure that the selected filter cartridges meet any relevant industry regulations for safety and performance. This is particularly important for applications involving natural gas, where adherence to environmental and safety standards is mandatory.
What are The Maintenance & Replacement Factors
Maintenance and replacement factors for filter cartridges are critical to ensuring optimal performance and longevity. Regular monitoring of flow rates and pressure drops can indicate when a filter is becoming clogged or inefficient, prompting timely replacement. The operating environment, such as temperature and contaminants in the fluid or gas being filtered, also affects maintenance frequency. Proper cleaning and inspection can extend the life of reusable cartridges, while disposable ones should be replaced according to manufacturer recommendations, often based on hours of operation or pressure drop criteria. Additionally, maintaining accurate records of filter replacement schedules and performance metrics helps in planning maintenance activities and ensuring compliance with industry standards.