One the most essential components in fuel gas processing is a fuel gas knockout drum. The knockout drum is designed to remove liquid droplets from the gas stream. As fuel gas passes through the drum, the heavier liquid falls out of the gas either due to gravity or they are captured by internal components, such as demister pads or vane packs. By this, the downstream equipment is preserved by preventing the contaminants from entering. The contaminants could cause corrosion, inefficiencies and fouling and by effectively capturing these impurities, knockout drums play a large role in reducing emissions. The removal of liquid before combustion or further processing ensures a cleaner burn, minimizes the release of pollutants, and helps operators meet regulatory standards for air quality.
Role of Demister Pads in Emission Control
Demister pads play a very important role in the emission control capabilities of knockout drums by enhancing the separation of liquid droplets from the fuel gas stream. These pads are generally installed inside the knockout drum. These fine mesh pads help in capturing and coalescing tiny liquid droplets that would otherwise escape with the gas flow. As the gas passes through the demister pad, small droplets adhere to the pad’s fibers and combine to form larger droplets. This then falls out of the gas stream due to gravity. This entire process significantly reduces the potential for liquid carryover, which is a major cause for downstream corrosion and inefficiencies.
By the process of preventing these contaminants from reaching combustion or processing equipment, demister pads contribute to a cleaner fuel gas output. This directly translates to reduced emissions. The high efficiency of demister pads captures even the smallest droplets and helps operators maintain compliance with air quality standards and supports a more environmentally friendly operation.
Comparison of Demister Pad and Vane Pack Separator

Demister pads and vane pack separators are both commonly used in knockout drums. However, they differ in design, separation efficiency, and suitability for varying operational conditions.
Demister pads are typically made using a fine mesh material that allows them to capture very small liquid droplets. This design makes demister pads highly effective at handling low to moderate gas flow rates and lighter liquid loads. Ideal for applications where fine mist separation is crucial. On the contrary, their dense structure can lead to higher pressure drops and potential clogging in cases of high particulate content.
Vane pack separators, on the other hand, consist of closely spaced, angled plates or vanes that redirect the gas flow in a zigzag pattern. This causes liquid droplets to impinge on the vane surfaces and then drain off. This structure allows vane pack separators to handle higher gas velocities and heavier liquid loads more efficiently with a lower risk of clogging than their counter parts – the demister pads. But on the downside, they are generally less effective than demister pads at capturing very fine mist, as their design is better suited for larger droplets.
Towed with this information, you can make the correct choice of choosing between a demister pad and a vane pack separator. Keep in mind factors such as gas flow rate, liquid load, and droplet size. For low-flow applications that needs fine mist removal, a demister pad may be the better choice. For high-flow applications or those with heavy liquid content, a vane pack separator is often preferable due to its ability to manage large volumes with minimal pressure drop.
Impact of Knockout Drums on Air Quality and Compliance
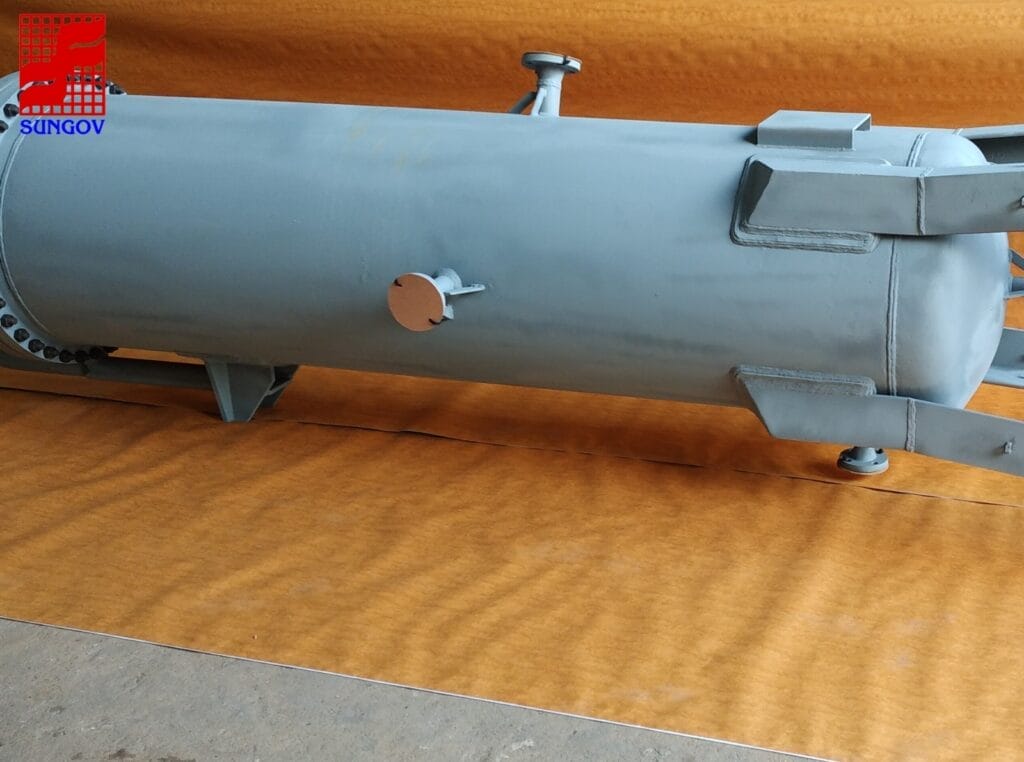
For reducing emissions and for supporting air quality improvement targets in the fuel gas processing, it is very important to effectively manage knockout drums. By the process of capturing liquid droplets, aerosols, and particulates before they enter the combustion or distribution process, knockout drums play a very important part in preventing these contaminants from becoming airborne pollutants. This separation process enhances the efficiency and lifespan of downstream equipment and minimizes the release of harmful emissions, including volatile organic compounds (VOCs) and other pollutants into the atmosphere. As environmental regulations become increasingly stringent, maintaining high-performance knockout drums is the major crux of achieving and sustaining emission limits compliance.
It is vital to use the correct configuration of knockout drums. This is achieved by selecting the right type of separator (demister pads or vane packs) and optimizing design for specific gas flow and liquid content. This enables companies to capture a greater range of particulates and mist. It also offers the flexibility to tailor separation solutions to a specific processing need, thus ensuring maximum emission control and regulatory compliance. By reducing carryover and improving separation efficiency, well-configured knockout drums enable operations to stay within permitted emission thresholds and avoid costly penalties, and along with this it also demonstrates a company’s commitment to environmental stewardship.
Sungov Engineering’s Role in the Manufacture of Knockout Drums
Sungov Engineering’s knockout drums are products that are designed with precision and advanced separation technology to ensure maximum efficiency in removing liquid droplets and particulates from fuel gas. Our drums incorporate high-quality demister pads and vane pack separators that effectively capture impurities, reduce carryover and play a huge part in supporting emission control.
Built to handle a range of gas flows and liquid loads, Sungov Engineering’s knockout drums help companies meet stringent environmental regulations while maintaining optimal performance in fuel gas processing. With robust designs and customizable configurations, our products are reliable solutions for cleaner operations and improved air quality compliance.